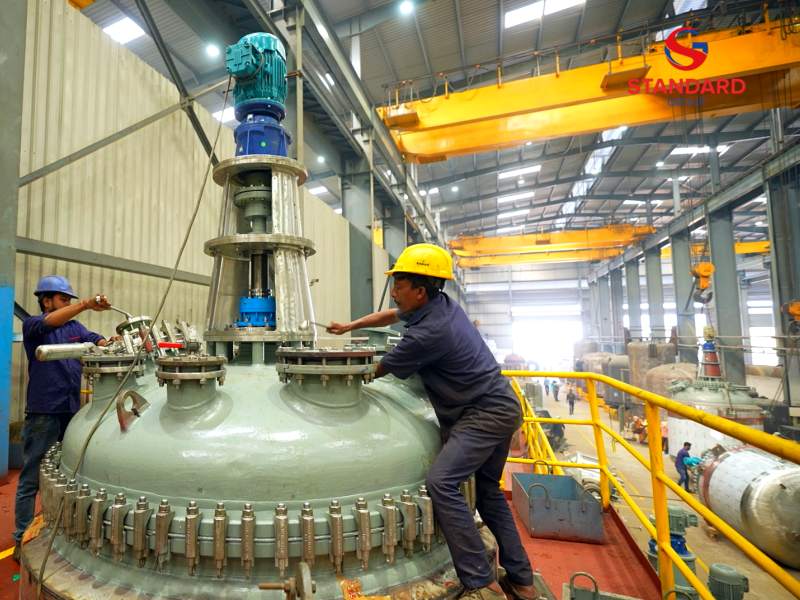
Glass-lined equipment plays a critical role in chemical, pharmaceutical, and high-purity process environments. Its ability to resist corrosion, prevent contamination, and perform under extreme conditions makes it the material of choice for mission-critical operations. However, its performance relies not only on the material itself, but on how meticulously it’s manufactured and tested.
At Standard Glass Lining Technology, quality assurance isn’t just a protocol—it’s a core operating principle that governs every stage of production. From materials selection to final inspection, every step is built around ensuring safety, compliance, and longevity.
Quality begins with structure. Standard Glass Lining Technology is certified to ISO 9001:2015, a globally recognised quality management standard. This certification ensures that all systems, processes, and documentation meet the highest levels of consistency, accountability, and continuous improvement.
ISO 9001:2015 compliance supports:
This structure empowers SGL to deliver equipment that meets international expectations for reliability and safety—every single time.
In addition to ISO certification, Standard Glass Lining Technology complies with stringent global manufacturing codes, including ASME (American Society of Mechanical Engineers) and DIN (Deutsches Institut für Normung).
These standards define parameters for:
By aligning its products with these standards, SGL ensures that clients receive equipment engineered not just for local compliance, but for global deployment.
A vital part of quality assurance at Standard Glass Lining Technology is the use of Inspection Test Plans (ITPs). These detailed documents outline every critical inspection point throughout the equipment's manufacturing life cycle.
Key checkpoints typically include:
Each step is carefully documented, signed off by qualified personnel, and made available to clients for complete transparency. These quality plans are not only about preventing defects, they’re about building confidence.
One of the most effective safeguards in modern equipment manufacturing is material traceability. Knowing exactly where each component originated from and how it was processed this is crucial for validating quality, ensuring safety, and supporting regulatory audits.
Standard Glass Lining Technology maintains complete traceability for all metallic and non-metallic components, including:
Each batch is tracked from procurement to installation using heat numbers, batch codes, and supplier certifications. In the event of a performance query or a third-party audit, all material documentation is readily available.
Once fabrication and lining are complete, a rigorous inspection and testing regime begins. This process is designed to confirm that the final product matches the design intent and is ready for years of dependable service.
Standard Glass Lining Technology conducts a wide range of inspections, including:
All tests are carried out by qualified inspectors using calibrated instruments. Detailed reports are provided to the client, creating a permanent quality record for each unit delivered.
While inspection is crucial, quality can’t be inspected into a product—it must be built in from the beginning. That’s why Standard Glass Lining Technology has cultivated a company-wide culture of quality ownership. From production staff to senior engineers, every team member understands the role they play in achieving manufacturing excellence.
This includes:
By embedding quality at every level, SGL ensures its equipment performs with reliability across decades of service, even in demanding industrial environments.
When your operation depends on glass-lined equipment, every detail matters—from the integrity of the welds to the purity of the lining. Standard Glass Lining Technology combines international compliance, rigorous testing, and complete traceability to deliver products you can trust.
Contact the Standard Glass team today to discuss how our quality-driven manufacturing approach can support your processing needs.