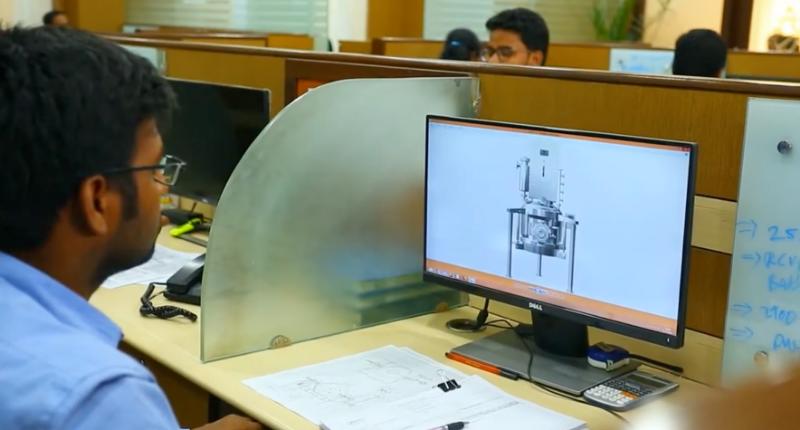
Modern manufacturing demands precision, especially when producing equipment for chemical and pharmaceutical industries. In designing glass-lined reactors, receivers, and storage vessels, accuracy is crucial. A slight misalignment can affect pressure tolerance, product flow or sealing integrity.
This is where 3D computer-aided design (CAD) has changed the game. At Standard Glass Lining Technology, 3D CAD is not just a design tool, it is a foundation for accuracy, repeatability and customisation. From concept to fabrication, 3D modelling drives innovation and consistency.
Traditional 2D drawings had limitations. Visualising complex geometry, testing component fit, or identifying clashes often required physical prototypes. With 3D CAD, designers at Standard Glass Lining Technology can visualise every element before production. This prevents costly mistakes and improves speed to market.
Designers can:
This level of visual and technical detail means fewer modifications during fabrication. It also improves collaboration across engineering teams and with clients, especially when changes are required during the review process.
Clients want assurance that their equipment will meet process requirements and site conditions. 3D models offer a clear visual representation of the final product. Clients can see port locations, manways, jacket placement and support legs in full context.
At Standard Glass Lining Technology, this has proven valuable when designing for constrained spaces or integrating new vessels into existing production lines. Instead of relying on measurements and interpretation, clients can review detailed renderings, animations or walkthroughs of the equipment before production begins.
This reduces misunderstandings, speeds up approvals and builds confidence in the final result.
In many industrial plants, flexibility is key. As production demands change, having modular systems allows for easier expansion, replacement or reconfiguration. 3D CAD supports this by enabling parametric modelling, where components can be reused, resized or repositioned without starting from scratch.
Modular design benefits include:
For example, Standard Glass Lining Technology can design modular skid-mounted units, where vessels, pipework and instrumentation are integrated into a compact frame. These systems can be shipped fully assembled, saving time during installation.
Using 3D CAD, the entire module can be digitally assembled and tested for mechanical compatibility and piping clearance. Clients can visualise how a modular setup will look and function, even before the first weld is made.
Standard Glass Lining Technology has delivered numerous projects where 3D CAD played a critical role in meeting complex requirements. One such case involved a pharmaceutical manufacturer seeking a custom reactor and receiver assembly that could fit within a legacy cleanroom with limited ceiling height.
Using 3D CAD, engineers modelled various configurations and validated nozzle positions to avoid structural clashes. By digitally testing disassembly and reassembly for maintenance, the team ensured the system could be serviced without dismantling nearby equipment.
Another project required a glass-lined heat exchanger integrated with a chemical reactor in a high-corrosion environment. CAD tools allowed the team to design a bespoke support structure that minimised vibration and facilitated thermal expansion, extending the service life of both vessels.
These successes were made possible through close client collaboration, detailed modelling and the flexibility 3D CAD provides in design iterations.
At the heart of these innovations is a disciplined design process. Standard Glass Lining Technology uses 3D CAD across every stage of equipment development, from concept sketches to final fabrication drawings.
Key features of the company’s design process include:
This structured approach ensures that every product meets dimensional tolerances, glass-lining standards and client expectations.
Mistakes in design often show up during fabrication or commissioning. By resolving these issues during the digital phase, 3D CAD reduces production errors. This leads to:
At Standard Glass Lining Technology, fewer surprises during assembly mean smoother project execution and greater confidence in the final product.
3D CAD is not just about creating visuals. It provides a framework for smarter manufacturing. Designs can be adapted for automation, digital twins, or future upgrades. Equipment created today can be referenced years later with full traceability and reproducibility.
As process industries continue to evolve, the ability to deliver customised, reliable and compliant solutions will remain a core advantage. Standard Glass Lining Technology’s investment in advanced design tools ensures they stay ahead of that curve.
When your operation relies on glass-lined equipment, consistency, safety and performance are non-negotiable. From the selection of raw materials to the final inspection, every product from Standard Glass Lining Technology reflects a commitment to precision and durability.
Contact the Standard Glass team today to explore how our expertise in high-quality, glass-lined manufacturing can enhance the reliability and efficiency of your operations.