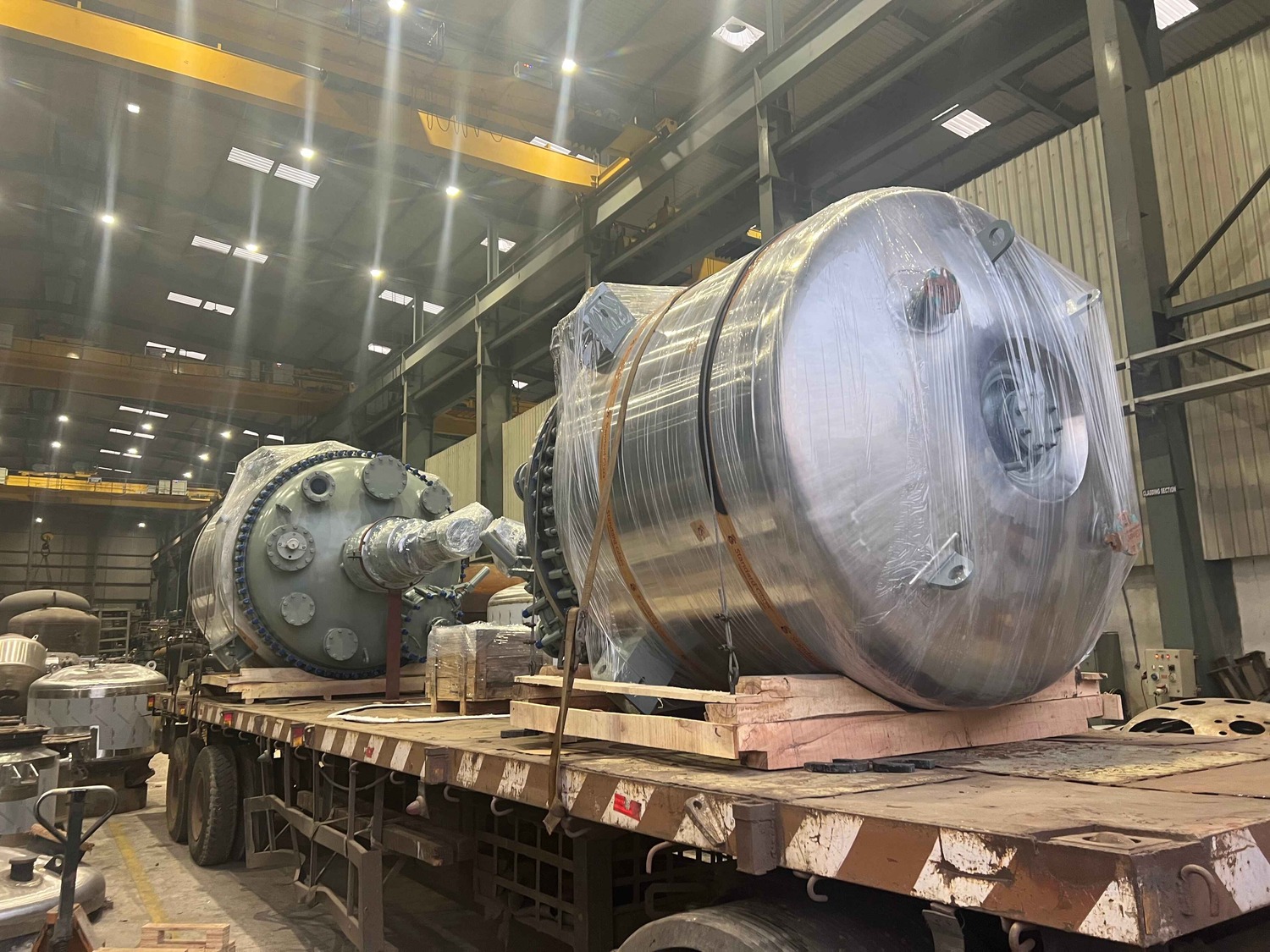
Stainless Steel was invented in 1912 by Harry Brearley of the Brown-Firth research laboratory in Sheffield, England (Standard Glass Lining Technology Ltd. UK home city). Mr Brearley was looking for a corrosion-resistant alloy for gun barrels when he discovered and subsequently industrialised the martensitic stainless steel alloy. Since then, Stainless steel has been adopted for containment of chemical processing because it has better chemical resistance than iron or mild steels.
Stainless Steel is an inorganic chemical combination of essentially iron, chromium and nickel. Products manufactured from stainless steel are strong and their initial cost, though higher than iron or mild steel, is often less than other exotic metallurgical materials. However Stainless can be misapplied which results in processing problems as the material does not have sufficient properties to overcome chemical attack or the corrosive attack of biofilm components. Unfortunately, Stainless steel will corrode over time as the minor ingredients are lost and as electrochemical potentials arise which promote the oxidation of iron.
This is typically illustrated in stainless steel weldments where the iron is made more readily accessible to oxidation. Even the “mildest” of chemical conditions such as hot steam, the resulting rust (“rouging”) will then contaminate and compromise the quality of the products being produced in such equipment.
Stainless steel can be chemically treated (passivated) to be made less reactive but this is a time consuming and expensive treatment that must be performed regularly to ensure that the iron in this material doesn’t oxidize (rust). The material can also be electro-polished but again this is expensive and can only ever be considered as a temporary improvement solution as electro-smoothing only miniaturizes the height of the asperities in the metallurgical surface and does little to remove the nooks and crannies surrounding the base of the asperities. Worse still, electropolishing can remove inclusions in the metal creating pits, which, in turn, can harbor microorganisms and biofilm components to perfectly shelter them from even the most vigorous cleaning.
Therefore in summary, no matter what treatment is made to stainless steel, unfortunately it is reactive to many harsh chemicals as encountered in pharmaceutical and biotechnologic applications and therefore alternate chemical resistance solutions must be applied to processing equipment.
Glass Lined equipment provides an idealised technical solution for chemical processing applications. The glass lining solution involves applying a chemical resistant enamel coat on a tough, durable substrate material such as Carbon Steel. This provides a cost effective, highly chemical resistant equipment solution that can be applied to almost all chemical processing applications, specifically those involving heat and pressure, as found in Reactor duties.
For further information about exceptional glass lining chemical resistance technology, please contact Standard Glass Lining Technology.