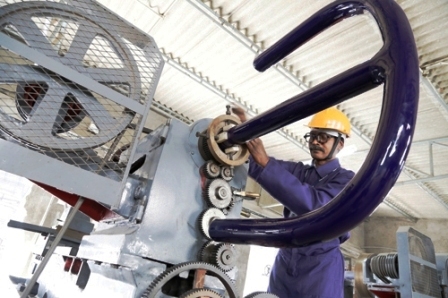
Stainless Steel was invented in 1912 by Harry Brearley of the Brown-Firth research laboratory in Sheffield, UK, the home of Standard Glass Lining Technology’s (UK). Mr Brearley was looking for a corrosion-resistant alloy for gun barrels when he discovered and subsequently industrialised the martensitic stainless steel alloy. Since then, stainless steel has been adopted for containment of chemical processing because it has better chemical resistance than iron or mild steels and is widely available in the market place.
Stainless Steel is an inorganic chemical combination of essentially iron, chromium and nickel. Products manufactured from stainless steel are strong and their initial cost, though higher than iron or mild steel, is often less than other exotic metallurgical materials. However Stainless can be misapplied which results in processing problems as the material does not have sufficient properties to overcome chemical attack or the corrosive attack of biofilm components. Unfortunately, Stainless steel will corrode over time as the minor ingredients are lost and as electrochemical potentials arise which promote the oxidation of iron.
This is typically illustrated in stainless steel weldments where the iron is made more readily accessible to oxidation. Even the “mildest” of chemical conditions such as hot steam, the resulting rust (“rouging”) will then contaminate and compromise the quality of the products being produced in such equipment. This can have disastrous consequences for pharmaceutical plants processing expensive drugs and human consumption related substances.
Stainless steel can be chemically treated (passivated) to be made less reactive but this is a time consuming and expensive treatment that must be performed regularly to ensure that the iron in this material doesn’t oxidize (rust). The material can also be electro-polished but again this is expensive and can only ever be considered as a temporary improvement solution as electro-smoothing only miniaturizes the height of the asperities in the metallurgical surface and does little to remove the nooks and crannies surrounding the base of the asperities. Worse still, electro polishing can remove inclusions in the metal creating pits, which, in turn, can harbor microorganisms and biofilm components to perfectly shelter them from even the most vigorous cleaning.
Therefore in summary, no matter what treatment is made to stainless steel, unfortunately it is reactive to many harsh chemicals as encountered in chemical, pharmaceutical and biotechnology applications and therefore alternate chemical resistance solutions must be applied to processing equipment.
Glass Lined equipment provides an idealised technical solution for chemical and pharmaceutical processing applications. A glass coating is sprayed then thermally fused onto the surface of substrate material, typically steel, at high temperature in a repetitive process until the desired glass thickness is achieved. The substrate material provides high strength to the equipment whilst the glass lining provides significant physical and chemical advantages for the wetted surfaces.
These glass lined wetted surfaces are hard wearing and highly polished making them easy to sustainably clean with a whole range of substances including steam. This super hard, fine finish also makes glass lined equipment surfaces inherently good at avoiding cross contamination in batch processing applications and as the glass finish does not affect the flavour, colour or purity of contents of equipment, it provides a very versatile solution for high quality operations.
Arguably the greatest advantage of glass lined equipment is the very high corrosion resistance against inorganic acid, organic acid and organic solvents at different concentrations and temperatures. As a result, glass lined equipment such as Reactors, Receivers and Storage Tanks have won favour with many plant managers across the UK, Europe, India and USA as the vessels are robust, durable, hard wearing and physically strong, capable of handling a wide range of high pressures and temperatures.
Traditionally, high quality glass lined equipment for Indian pharmaceutical applications had to imported from suppliers in Europe and North America. This made the widespread use of glass lined equipment, specifically for bespoke equipment, in India, commercially restrictive. However, over the last 5 years with the introduction of Standard Glass Lining Technology Pvt. Ltd. based in Hyderabad, world class glass lined technology for ALL types of process equipment and associated components has become very affordable for the Indian domestic market.
Standard Glass Lining Technology is part of the Standard Group of Companies with primary manufacturing facilities of over 250,000sqft based in Hyderabad in over eight facilities, with technological innovation from the UK. The company therefore supplies a whole host of turnkey advantageous equipment designs from Valves to Reactors, Filters to Blenders and Barrier Isolators to Agitated Nutsche Filter Dryers (ANFD's), any of which can be offered with glass lined wetted surfaces.
The result is an affordable, superior performing glass lined product range, ideal for holistic chemical and pharmaceutical processes, which offers increased equipment durability, hardness and chemical resistance compared to other materials, delivered with exceptional customer service.
For further information about high quality, glass lining chemical resistance technology, and/or the wide range of world class equipment designs the Standard Group provide, please contact Standard Glass Lining Technology here.