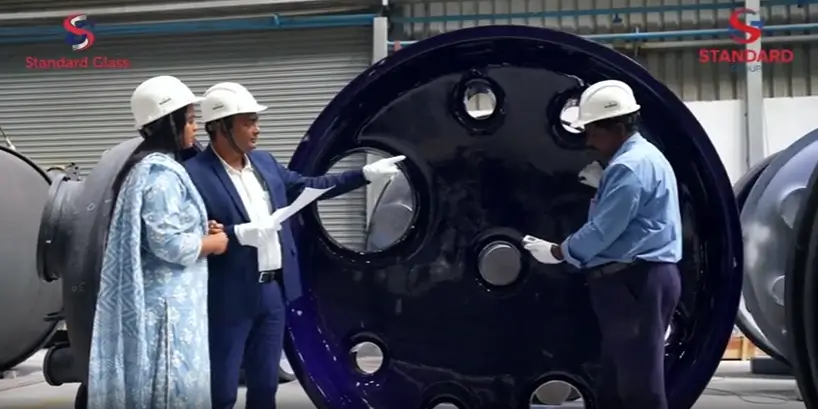
At Standard Glass Lining Technology, excellence is not a goal, it’s a guarantee. Nowhere is this more evident than in the production of glass-lined heat exchangers, where the smallest deviations in geometry can lead to major inefficiencies or failures. That’s why SGL applies its industry-leading precision technology to every stage of heat exchanger manufacturing, delivering not only reliability but also performance that meets the highest industrial standards.
Glass-lined heat exchangers are often deployed in highly sensitive chemical and pharmaceutical environments. These components must handle corrosive substances, withstand temperature extremes, and maintain flow efficiency. Any discrepancy in shape, thickness, or alignment can compromise:
By using precision engineering to control these variables, Standard Glass Lining Technology ensures that its glass-lined heat exchangers are both high-performing and dependable in the field.
Heat exchangers are complex assemblies involving bundles of tubes, baffles, shells, and heads. Each element must conform to tight geometric tolerances for the exchanger to function efficiently. Even slight variations in:
can create resistance to flow, cause uneven heating, or introduce stress points.
SGL’s precision inspection processes—including laser metrology, CMM scans, and automated measuring arms verify that each component stays within exact dimensional limits. This accuracy ensures optimal fluid dynamics and consistent performance across varying batch conditions.
Glass lining adds another layer of complexity. The fusion of enamel to steel alters the thermal and geometric profile of components. Without precise control, the lining process could warp tubes, affect surface finish, or distort key geometries.
To counter this, SGL employs:
The result is a fully lined heat exchanger that performs under pressure—without compromise.
Precision isn’t just about individual components. It’s also about how those parts come together. The accurate alignment of tube sheets, for instance, affects both the ease of assembly and the effectiveness of thermal transfer. By maintaining tight tolerances, SGL ensures:
For customers, this translates to fewer operational issues and reduced maintenance downtime.
In glass-lined heat exchangers, the interfaces between flanges and gaskets are crucial for safe operation. Irregular surfaces or non-uniform roundness can cause sealing failures, leading to leaks or contamination.
Standard Glass Lining Technology uses roundness detection tools and flatness verification equipment to make sure sealing surfaces are perfectly aligned. This guarantees:
Fluid dynamics play a key role in heat exchanger performance. Flow paths must be carefully controlled to prevent stagnation zones, fouling, or inefficient heat transfer. Precision in the spacing of tubes, diameter consistency, and the alignment of flow baffles helps maintain predictable, streamlined movement.
SGL’s dimensional accuracy ensures that each unit operates at peak efficiency—improving energy transfer, reducing operational costs, and supporting process repeatability.
Why It Matters to Critical Process Industries
In industries like pharmaceuticals, chemicals, and agro-processing, production relies on consistency. Heat exchangers play a role not just in temperature control, but also in the overall safety and effectiveness of the production environment.
With its focus on geometric accuracy and tolerance control, Standard Glass Lining Technology helps customers in these industries:
More efficient heat transfer means less energy waste. SGL’s attention to precision enhances the environmental performance of its equipment. With tighter tolerances, every exchanger:
This aligns with broader industry moves toward greener, more responsible manufacturing—something SGL has long championed.
Validated Quality, Delivered with Confidence
Every glass-lined heat exchanger from SGL is supplied with full dimensional and QA documentation. Clients receive traceable proof of compliance with ISO, ASME, and customer-specific requirements.
Key documents include:
This level of transparency reinforces trust and makes integration with internal quality systems seamless.
Standard Glass Lining Technology doesn’t just build heat exchangers—it engineers them to outperform. And with continual investments in metrology, robotics, and digital QA systems, SGL is setting the new benchmark for glass-lined equipment precision.
If your operation depends on clean, reliable, high-performance thermal systems, SGL’s precision advantage delivers measurable results.
Interested in exploring how precision can improve your heat exchanger reliability? Contact the team at Standard Glass Lining Technology today. Discover how our accuracy-first approach is reshaping what’s possible in process equipment.