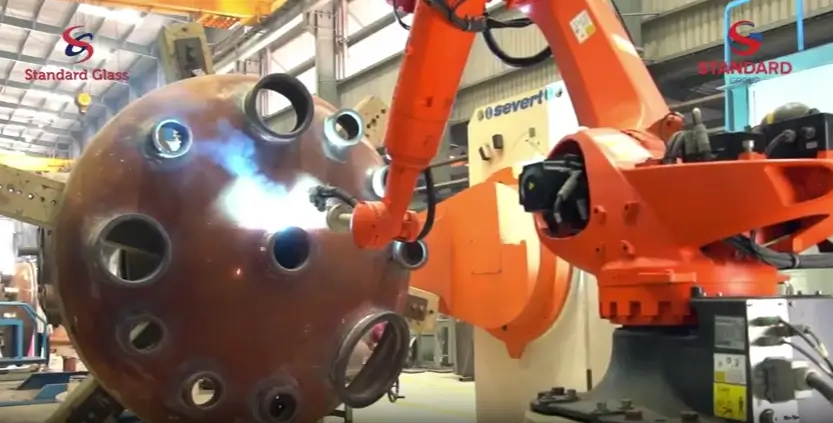
Accuracy matters—especially when it comes to manufacturing equipment for industries where quality cannot be compromised. That’s why Standard Glass Lining Technology has invested heavily in the latest precision technology to refine every aspect of its production process.
From the exact geometry of vessels to the consistent roundness of components, SGL ensures every product meets the highest dimensional standards. This not only guarantees superior performance but also enhances safety, reduces waste and improves compatibility in mission-critical environments.
When producing reactors, columns, and vessels for use in pharmaceutical, chemical, and food industries, the slightest deviation in shape or size can lead to costly issues. Improper roundness or geometric misalignment can compromise:
At Standard Glass Lining Technology, achieving and maintaining tight tolerances isn’t optional—it’s an integral part of delivering durable, reliable, and regulatory-compliant equipment.
To achieve consistent precision, Standard Glass Lining Technology adopts a holistic approach. It starts with state-of-the-art CAD modelling and finishes with multi-point inspection. Every stage of the process is underpinned by cutting-edge metrology and real-time monitoring systems.
This seamless integration allows SGL to:
SGL’s quality assurance teams employ advanced Coordinate Measuring Machines (CMMs), laser scanning, and 3D surface mapping tools. These devices offer micrometre-level accuracy when verifying geometric parameters such as:
This precision ensures that the final product matches exact specifications not just in isolation, but when assembled into broader processing systems.
Automation plays a significant role in SGL’s precision strategy. Robotic handling systems, automated weld positioning, and CNC machining are all deployed to reduce the chance of human error.
By automating key steps, Standard Glass Lining Technology achieves:
As a result, customers benefit from equipment that performs exactly as expected—every time.
One of the most critical parameters in pressure vessels and reactors is roundness. Even minor irregularities can compromise gasket sealing, leading to leaks, contamination, or safety hazards.
SGL’s equipment undergoes rigorous circularity inspections. Each vessel is measured at multiple points to confirm that it adheres to strict roundness specifications. This not only supports compliance with pressure equipment directives but also enhances durability and process reliability.
Maintaining precise dimensions becomes even more complex when applying a glass lining. The fusion of glass to steel requires careful control of thickness, adhesion, and shrinkage.
To manage this, Standard Glass Lining Technology uses:
These technologies ensure that the glass layer remains consistent and doesn’t distort the underlying geometry. The result is a product with both functional performance and dimensional fidelity.
Precision doesn’t begin and end with final inspection—it’s baked into every stage of SGL’s manufacturing:
This level of detail creates equipment that fits precisely within process systems, reduces installation time, and supports long-term operational efficiency.
Customers of Standard Glass Lining Technology receive more than just finished equipment—they gain access to detailed inspection records and conformity reports. These documents provide traceable evidence of dimensional compliance and help clients meet their own internal and regulatory QA requirements.
From batch certifications to geometric deviation maps, SGL provides full transparency, supporting confidence at every stage of the procurement cycle.
Precision has another often overlooked benefit—interchangeability. Whether replacing a component or upgrading part of a production line, dimensional consistency ensures that new parts integrate smoothly with existing systems.
This reduces the need for costly custom modifications and minimises downtime during maintenance or scale-up.
Standard Glass Lining Technology doesn't just use advanced tools, it continually reinvests in them. Recent upgrades include:
By staying ahead of technological trends, SGL reinforces its role as a trusted partner in precision manufacturing.
Precision isn’t just about tools it’s about mindset. At Standard Glass Lining Technology, every team member is trained in the importance of accuracy, inspection, and process control. Through regular audits, training sessions, and cross-functional reviews, the company maintains a culture where quality is everyone’s responsibility.
This focus on continuous improvement ensures that clients always receive the most advanced, reliable, and compliant solutions possible.
From geometric tolerances to perfect roundness, the precision engineering capabilities of Standard Glass Lining Technology give customers an edge in today’s demanding industrial environments. With every product, SGL delivers not just technical excellence, but measurable performance.
Want to ensure your equipment meets the highest standards of accuracy and performance? Get in touch with the experts at Standard Glass Lining Technology to learn how precision technology can support your process goals.